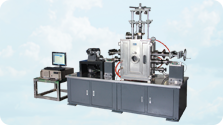
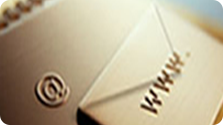



磨损是伴随着摩擦而产生的必然结果,是相互接触的物体相对运动时,表层材料不断发生损耗的过程或产生塑性变形的过程。磨损既是材料消耗的主要原因,也是影响机械使用寿命的主要因素。
一般磨损过程分为跑合阶段、稳定磨损阶段和剧烈磨损阶段。跑合阶段:在一定载荷作用下,摩擦副接触表面逐渐磨平,实际接触面积逐渐增大,磨损速率开始时较大,而后减缓。稳定磨损阶段:摩擦表面经过跑合后相互适应,达到稳定状态,摩擦降低,磨损量保持不变,是摩擦副的正常工作阶段。剧烈磨损阶段:摩擦副长期工作后,表面性质发生变化,磨损量迅速增大,引起摩擦表面剧烈磨损,从而导致失效。
磨损是多因素互相影响与作用的一个复杂过程,一般磨损作用的影响通过表面的作用、表层的变化和破坏形式来分析和研究。常用的磨损机理分析主要为黏着磨损、磨粒磨损、表面疲劳磨损、腐蚀磨损和微动磨损。
1. 黏着磨损
当摩擦副相对滑动时,由于黏着效应所形成的结点发生剪切断裂,被剪切的材料或脱落成磨屑,或由一个表面迁移到另一个表面的现象,称为黏着磨损。按磨损程度可分为:①轻微黏着磨损,黏着点强度低于摩擦副金属强度时,剪切发生在结合面上;②一般黏着磨损(涂抹),黏着点的强度高于摩擦副中较软金属的剪切强度时,破坏发生在离结合面不远的软金属表层内,软金属黏附在硬金属表面上;③胶合磨损,黏着点强度比两金属的剪切强度高得多,且黏着点面积较大时,剪切破坏发生在一个或两个金属表层较深的地方;④擦伤磨损,黏着点的强度高于摩擦副金属材料强度时剪切破坏主要发生在软金属的表层内,有时也发生在硬金属表层内,迁移到硬金属上的黏着物又使软表面出现划痕;⑤划伤磨损,黏着结合强度高于集体金属的抗剪切强度,切应力高于黏着结合强度。
2. 磨粒磨损
在摩擦过程中,硬的颗粒或硬的凸出物冲刷摩擦表面引起材料脱落的现象称为磨粒磨损。磨粒磨损又分为:①二体磨粒磨损,磨粒沿一个固体表面相对运动时产生的磨损;②三体磨粒磨损,外界磨粒移动与两摩擦表面之间的磨损。磨粒磨损的机理主要为:①微观切削,法向载荷将磨粒压入摩擦表面,滑动时的摩擦力通过磨料的犁沟作用使表面剪切、犁皱和切削,产生槽状磨痕;②挤压剥落,磨料在载荷作用下压入摩擦表面而产生压痕,将塑性材料的表面挤压出层状或鳞片状剥落碎屑;③疲劳破坏,摩擦表面在磨料产生的循环接触力作用下,使表面材料因疲劳而剥落,破坏源离表面近,具有组织敏感性,疲劳破坏具有局部性;④微观断裂,摩擦表面在磨料产生的循环接触力作用下,使表面材料因疲劳而剥落,破坏源离表面近,具有组织敏感性。
3. 表面疲劳磨损
表面疲劳磨损是指两个相互滚动或者滚动兼滑动的摩擦表面,在循环变化的接触应力作用下,由于材料疲劳剥落而形成凹坑,引起表面脱落的现象。在循环接触应力作用下,疲劳裂纹发源在材料表层内部的应力集中源。裂纹萌生后,先顺滚动方向平行于表面扩展,然后分叉延伸到表面,使磨屑剥落后形成凹坑,断口较光滑,裂纹形成迅速,但扩展缓慢。由于表层萌生疲劳破坏坑边缘可以构成表面萌生裂纹的发源点,所以,通常这两种疲劳磨损是同时存在的。点蚀磨屑多为扇形颗粒,凹坑为许多小而深的麻点。点蚀疲劳裂纹起源于表面,在顺滚动方向向表层内扩展,并形成扇形的疲劳坑。剥落磨屑呈片状,凹坑浅而面积大。剥落疲劳裂纹开始于表层内,随后裂纹与表面平行向两端扩展,最后在两端断裂。
4. 腐蚀磨损
在液体、气体或润滑剂的工作环境中,相互作用的摩擦表面之间会发生化学或电化学反应,在表面形成腐蚀产物,这种腐蚀产物黏附不牢,在摩擦过程中剥落下来,而新的表面又继续和介质发生反应,腐蚀磨损就是指这种腐蚀与磨损不断相互重复作用的现象。
5. 微动磨损
微动磨损是指两表面之间由振幅很小的相对振动产生的磨损。若在微动磨损过程中,表面之间的化学反应起主要作用,则成为微动腐蚀磨损,与微动磨损相联系的疲劳损坏,则成为微动疲劳磨损。在微动磨损过程中,接触压力使摩擦副表面的微凸体产生塑性变形和黏着,在外界小振幅振动作用下,黏着点剪切,黏着物脱落,剪切表面被氧化。由于两摩擦表面紧密配合,磨屑不易排出,起磨料作用,加速微动磨损。微动磨损的主要特征是摩擦表面上存在带色的斑点,其内集结着已压合的氧化物。微动磨损改变零件形状,恶化表面层质量,降低尺寸精度,使紧配合件变松,引起应力集中,形成微观裂纹,导致零件疲劳断裂。如果微动磨损产物难于从接触区排走,腐蚀产物体积膨胀,使局部接触压力增大,可能导致零件胶合,甚至咬死。